July 21, 2025
Hard-Facing vs. Carbide Overlay: A Technician’s Guide to Field Repairs on GET Attachments
Ground-engaging components like bucket lips, cutting edges, and ripper shanks operate in abrasive, impact-prone environments that erode steel, decreasing productivity and increasing costs. Hard-facing and carbide overlay are two cost-effective protection strategies for Pacific Truck & Tractor.
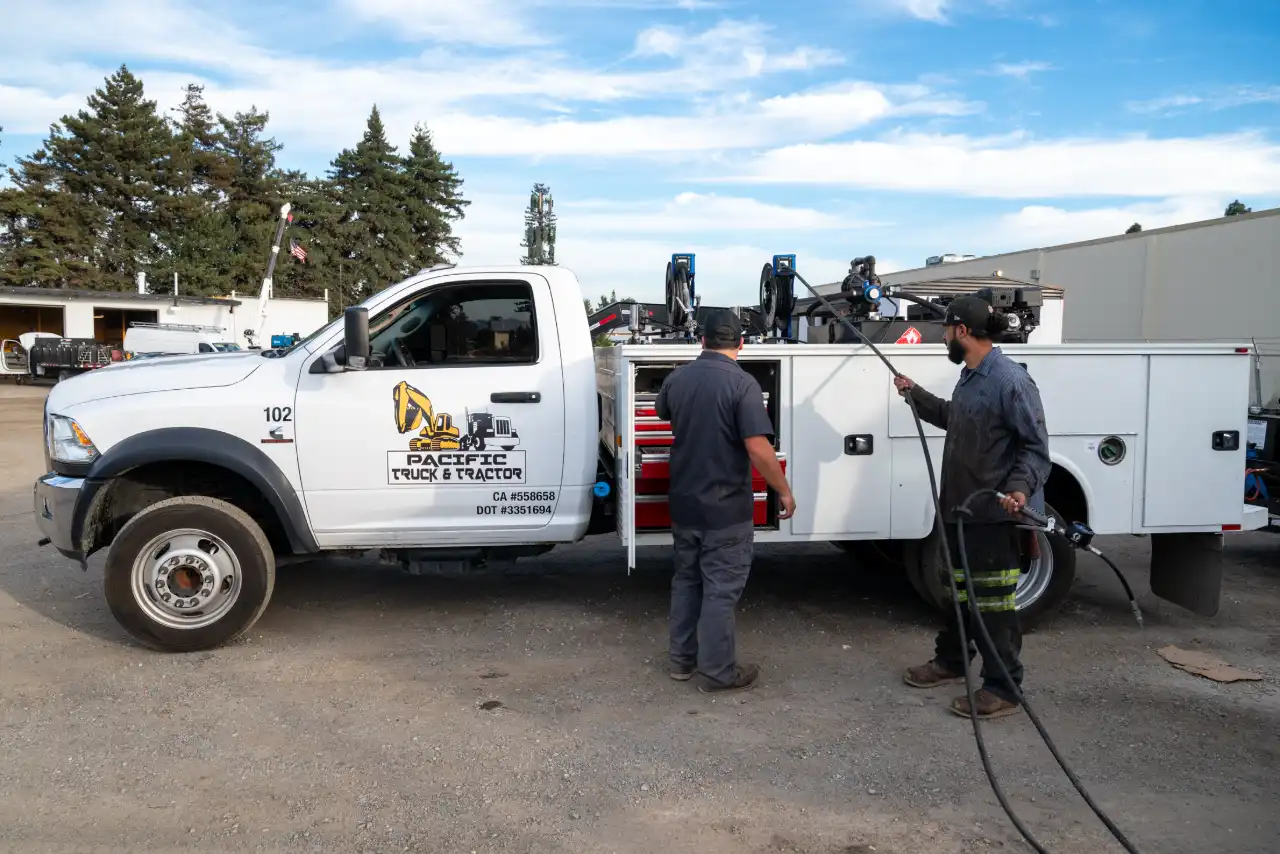
Ground-engaging components—such as bucket lips, cutting edges, ripper shanks, and similar wear parts—operate in an abrasive, impact-prone environment that constantly erodes steel. Unchecked wear decreases machine productivity, increases fuel consumption, and causes unplanned outages that disrupt project schedules. Two proven surfacing strategies—hard-facing and carbide overlay—offer cost-effective, field-ready protection. The following technical review provides a formal comparison of these processes, their metallurgical bases, decision criteria, and best-practice welding procedures relevant to Pacific Truck & Tractor’s clients in San Lorenzo, California.
Process Fundamentals
Hard-Facing
Hard-facing involves depositing a wear-resistant alloy—usually high-carbon, chromium carbide flux-cored wire—onto a steel substrate. The resulting martensitic matrix measures 55–60 HRC and comprises primary M₇C₃ carbides, which provide high abrasion resistance without becoming too brittle. Its versatility, affordable consumables, and compatibility with standard GMAW/FCAW equipment make hard-facing the leading choice for surfaces exposed to impact and abrasion.
Tungsten Carbide Overlay
A tungsten carbide overlay (TCO) embeds granular WC particles—up to 70% by volume—within a nickel- or iron-based matrix deposited through open-arc, PTA, or laser cladding methods. With composite hardness often exceeding 70 HRC, TCO provides excellent resistance to fine-particle erosion, sliding abrasion, and high-temperature wear. The downside is higher material cost and increased vulnerability to brittle fracture under concentrated impact.
Comparative Performance Metrics
Chromium carbide deposits resist impact and abrasion because of their more rigid matrix. In contrast, WC particles in TCO offer better sliding-wear protection but crack under repeated mechanical shock.
Decision Framework for Pacific Truck & Tractor Clients
- Soil and Aggregate Classification
- Cohesive loams and mixed rock demand the balanced hardness of hard-facing.
- Silica-rich sands, decomposed granite, or crushed felspar justify the use of carbide overlay, despite its higher cost.
- Tool Geometry and Section Thickness
- Slender bucket teeth or serrated lips are suitable for the lower dilution and bead profile of hard-facing.
- Broad grader blades or scraper floors accommodate the extra weight of TCO, allowing for longer service life.
- Planned Service Interval
- Projects targeting 800–1,200 operating hours between interventions can optimize life-cycle cost through hard-facing.
- Remote mining operations with change-outs every 3,000–4,000 hours gain financially from TCO.
- Economic Considerations
- A material cost multiplier of three is acceptable if TCO increases wear life by five, reducing downtime and logistics costs.
- Environmental Loads
- Heat-softening of chromium carbide films starts near 450 °C, while WC overlays maintain their hardness above 1,000 °C. Asphalt milling, slag handling, and furnace-charge duties therefore favour TCO.
Field Welding Protocol
Equipment Configuration
- Power Source: 300 A multi-process inverter with constant-voltage (CV) for FCAW and constant-current (CC) mode for SMAW buffer passes.
- Consumables:
- Hard-facing wire: 1.6 mm CrC FCAW, all-position, 30–45% carbide phase.
- TCO wire: 2.4 mm open-arc WC-filled composite or PTA-feed tungsten carbide powder.
- Pre-Heat:
- Minimum of 95 °C for low-alloy steels less than 50 mm.
- 150–200 °C for cast steels and high-manganese assemblies.
- Inter-Pass Temperature: Keep below 600 °C to maintain carbide hardness.
- Cooling: Passive air cooling only; forced quenching causes micro-cracking.
Step-by-Step Procedure
- Inspection and Dimensional Check: Verify that the worn component retains at least 50% of its original cross-sectional area. Components below this level should be replaced rather than resurfaced.
- Surface Preparation
- Oxy-fuel gouging or plasma-arc removes fatigued material and micro-cracks.
- Grind to a bright metal; final surface profile < 75 µm Ra ensures good fusion.
- Buffer Layer (if required): Apply austenitic-manganese or NiCrFe buttering pass on cast or high-carbon substrates. This reduces dilution and accommodates differential thermal expansion.
- Primary Deposition
- Hard-Facing: Deposit 10 mm overlapping stringer beads perpendicular to the material flow, using an alternating sequence to control heat input.
- TCO: Deposit 6–8 mm beads with minimal oscillation; use a double-layer strategy for optimal carbide density.
- Post-Weld Treatment
- Slag removal, visual inspection, and audible chipping-hammer test; a dull ring indicates a lack of fusion.
- Dress high spots to the original profile, maintaining OEM tooth rake angles to prevent inefficient digging.
Quality Assurance and Inspection
- Perform Magnetic Particle Examination (MT) on surface-breaking cracks immediately after cooling to ambient temperature.
- Portable Hardness Testing (UCI or Leeb) to verify target hardness range (≥ 55 HRC for hard-facing, ≥ 70 HRC for TCO).
- Dimensional verification using a contour gauge or Faro arm ensures that the bucket lip geometry stays within ±3 mm of the OEM specifications.
Environmental and Occupational Safety
Both processes emit hexavalent chromium and metal particulate fumes. Technicians must wear PAPRs equipped with P100 cartridges, flame-resistant clothing, and leather gauntlets. Work areas require local exhaust ventilation, achieving a minimum of 100 cubic feet per minute (ft³/min) per welder. Compliance with Cal/OSHA permissible exposure limits (PEL) is mandatory.
Cost-Benefit Illustration
A crawler excavator working on the Alameda Creek flood-control project uses three sets of bucket teeth each year, unless they are treated. Replacing each set, including downtime, costs about $5,000. Adding hard-facing extends the teeth's life to two sets annually, reducing the yearly cost to $3,600. Switching to TCO further prolongs the lifespan to one replacement per year, at a total cost of $7,200 (materials and welding), but it increases uptime by 40 machine hours. At a billable rate of $250 per hour, the additional production gained offsets the higher surfacing cost, resulting in a net saving of $3,800.
Conclusion
Both hard-facing and carbide overlay serve as durable, field-ready defences against abrasive wear of ground-engaging tools. Hard-facing offers an economical, impact-resistant barrier suitable for mixed-material construction sites. Tungsten carbide overlay, although more expensive, provides superior longevity in high-silica or high-temperature environments where downtime is costly. A structured selection matrix that considers soil composition, scheduled maintenance windows, and total cost of ownership helps ensure the best surfacing choices for heavy equipment fleets across the Bay Area.
Precisely engineered solutions reduce downtime and increase profitability. Contact Pacific Truck & Tractor to arrange on-site field welding repairs and receive a data-driven surfacing recommendation tailored to your operation.